- De la conception à la construction
- Le suivi 24/24 à distance
- La qualification
- La maintenance
- Les étapes de construction
- Les matériaux
- Les centrales de ventilation
- Les ISO 5
L’intégration en salle blanche électronique
Les chambres propres jouent un rôle crucial dans l’industrie électronique et micro électronique en offrant un environnement contrôlé exempt de particules de poussière et de contaminants. Ces salles propres électroniques sont conçues pour maintenir des niveaux extrêmement bas de particules en suspension, ce qui est essentiel pour la bonne fabrication de composants électroniques de haute précision. Les microprocesseurs, les puces mémoire et autres composants électroniques sont fabriqués dans ces environnements ultra-propres pour garantir des performances fiables.
La présence de poussière dans les circuits imprimés peut causer des problèmes majeurs, tels que des courts-circuits, des interférences électromagnétiques et des défaillances prématurées. Les particules de poussière peuvent également affecter la qualité des connexions et des soudures, ce qui compromet la fiabilité des appareils électroniques.
En conclusion, les salles blanches sont essentielles pour maintenir des normes élevées de qualité et de fiabilité dans l’industrie électronique et microélectronique, en assurant que les composants fabriqués sont exempts de contaminants susceptibles de compromettre leurs performances.
OplusR construit des salles pour le domaine de l’électronique, les panneaux sont rarement des panneaux sandwich avec de la laine de roche mais plus souvent en nid d’abeille, ce qui augmente très fortement le prix.
Sur un circuit intégré, des poussières d’une dimension de quelques micromètres pourraient être comparées à un éléphant dans un magasin de porcelaines… Cette contamination peut ruiner la viabilité des produits fabriqués. Afin de produire des composants sans contamination, il est nécessaire de travailler dans une zone sans contamination.
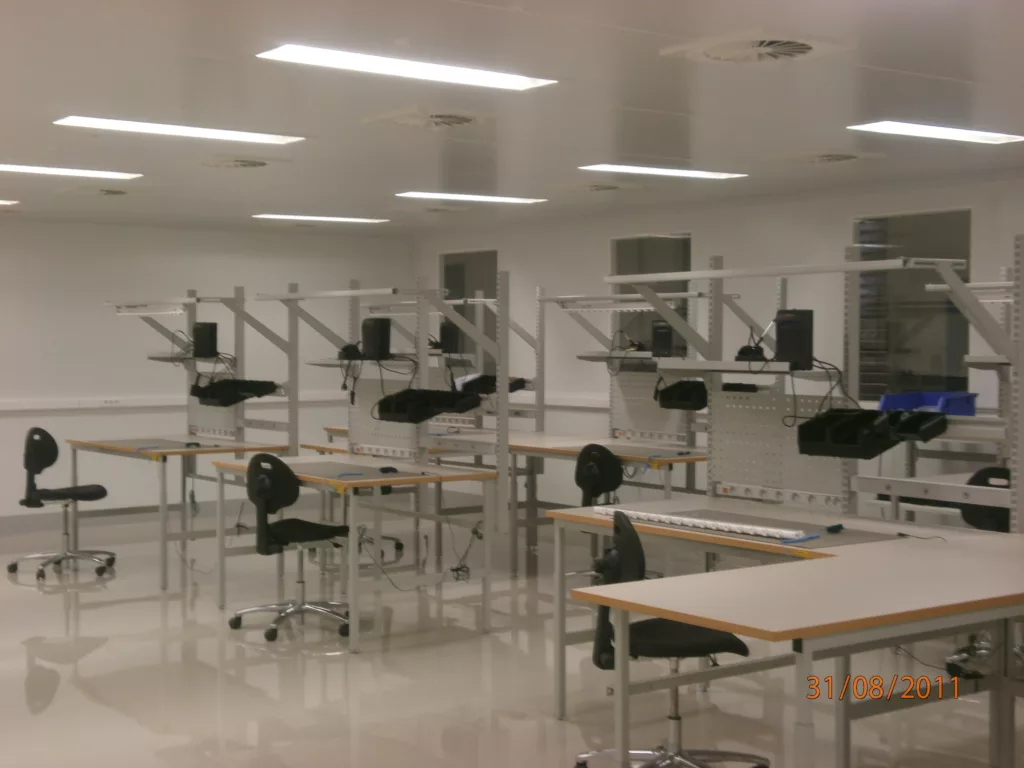
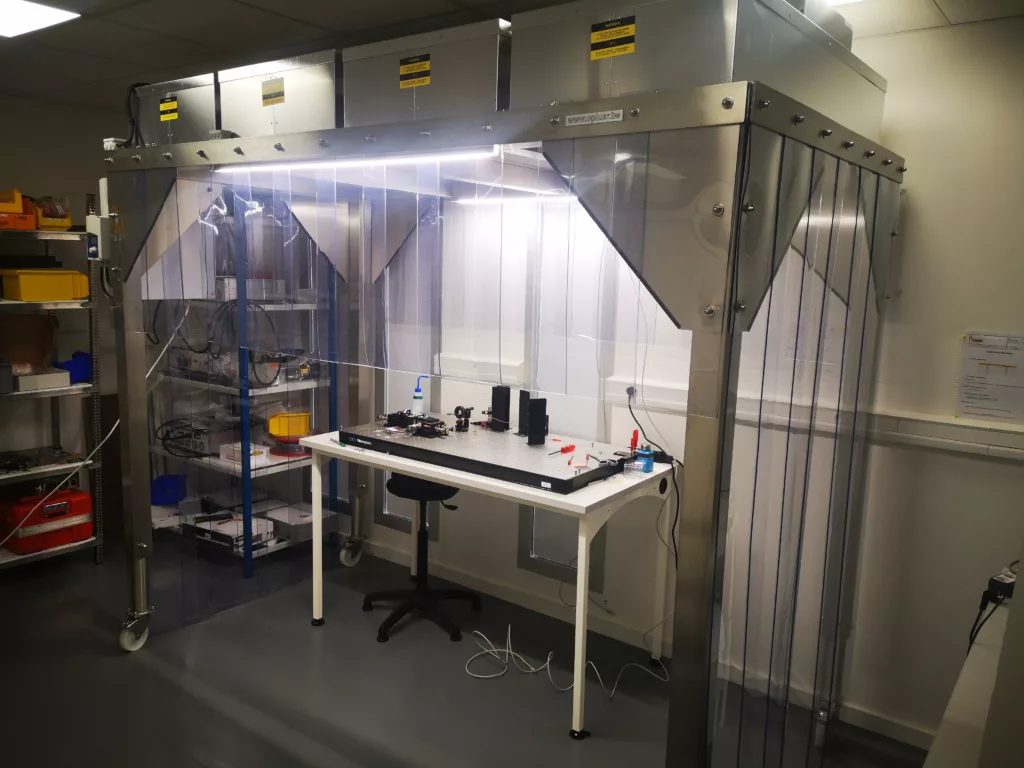
Produire des circuits intégrés en salle blanche
Les opérations de production se déroulent maintenant presque à un niveau moléculaire et la réussite dépend de la pureté des matériaux, mesurée en parts par trillion (= million de millions de millions). L’industrie de la microélectronique se base sur deux composants principaux : le germanium et le silicium. Ces matériaux sont semi-conducteurs càd qu’ils peuvent être dans un état conducteur du courant électrique ou pas.
La fabrication des circuits intégrés peut être divisée en trois étapes:
Matériaux
Au départ du sable de silice, les cristaux monocristallins sont fabriqués selon le Procédé de Czochralski. Cette étape ainsi que le nettoyage du creuset doivent être effectués en salle blanche ISO 5 au minimum (Classe 100). Toute contamination introduite durant ce processus causera des dégâts au niveau de la pureté du cristal et sera à l’origine de propriétés électriques inacceptables. Ensuite, le matériau sera travaillé pour obtenir la finition requise, l’épaisseur, la planéité,… Il faut prendre garde à ne pas inclure des éléments dopants malvenus sur la surface qui peuvent également mener à la modification ou suppression des propriétés électriques recherchées.
Fabrication des plaquettes de silicium
Il y a un grand nombre d’étapes pour transformer le cristal en plaquettes de silicium. Ce processus comprend des cuissons à 1100°C, des attaques chimiques, des radiations ioniques,… Ce processus complexe permet de fabriquer des éléments contenant chacun des millions de circuits actifs sur un centimètre carré. Les dimensions de ces circuits peuvent être de maximum 0,01 micron… La fabrication des plaquettes de silicium doit être réalisée dans une salle blanche de qualité Classe 100 minimum et de qualité égale ou supérieure à Classe 1 pour les étapes les plus critiques. Règle : la taille maximum d’une particule contaminante acceptable est 1/10ème de la dimension de la plus petite pièce critique.
Assemblage et test
Cette dernière phase regroupe les activités de test des plaquettes de silicium, leur séparation, leur montage sur un support, encapsulage, leur test,… Lors des phases précédentes, la contamination atomique et ionique a été prévenue. Généralement, ces phases sont réalisées dans des salles blanches d’une qualité entre l’ISO 7 et l’ISO 5. Lors de cette dernière phase, les produits finis doivent maintenant être protégés :
- des particules plus grandes qui pourraient induire des court-circuits entre conducteurs
- contre les décharges électrostatiques auxquelles ils sont vulnérables
- de l’huile ou tout autre matériau sur la surface qui empêche l’étanchéité ou l’adhésion d’un plastique ou d’une encre, qui empêche un bon contact électrique.
Nous suivre, nous joindre :
salle blanche électronique en France – Belgique – Luxembourg – Suisse
Atelier :
Zoning du Pétria,
6140 Fontaine L’Eveque
COPYRIGHT 2022-
Un site Web WordPress.